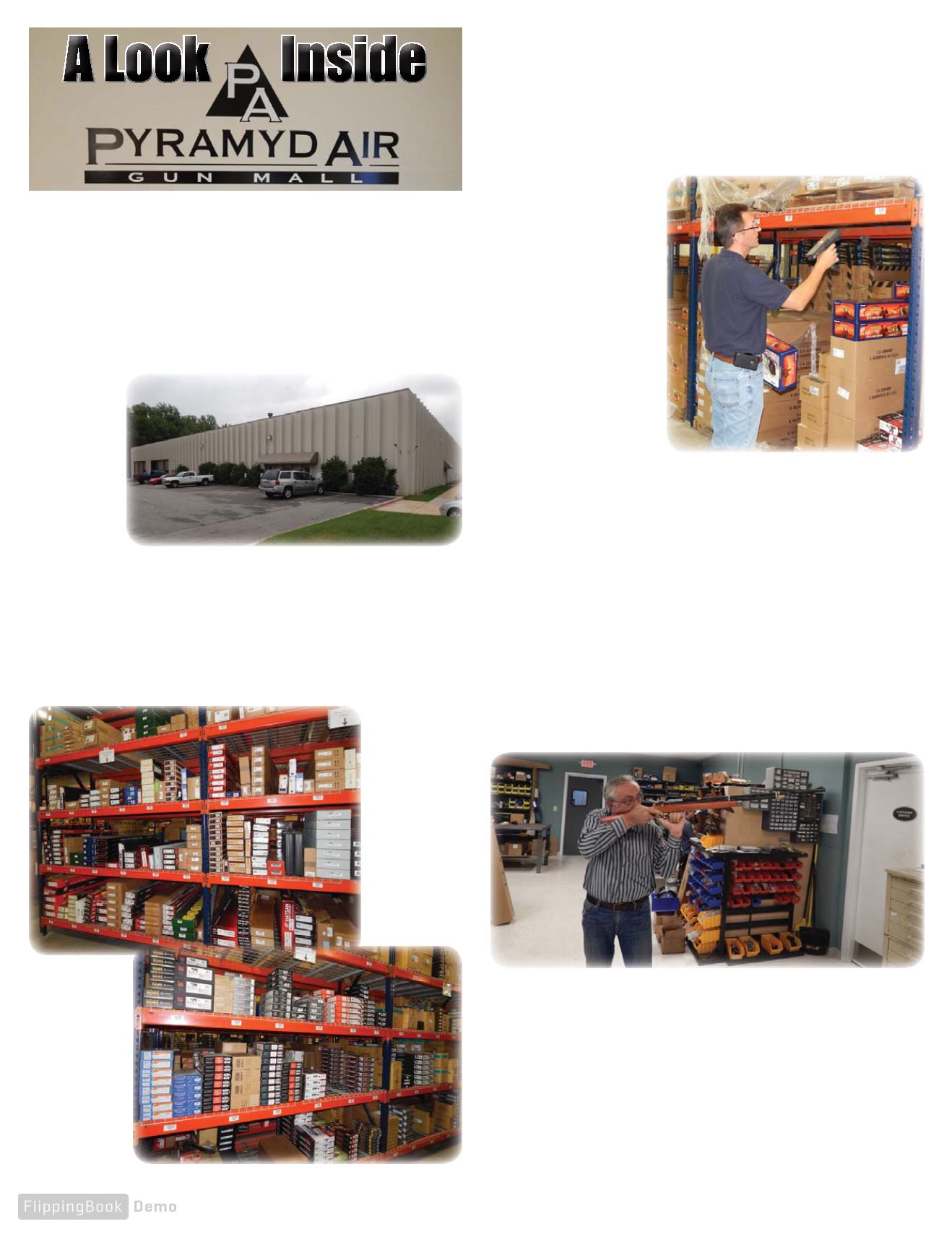
www.airgunhobbyist.com
Page 27
Organization is the key to being able to locate and
ship items quickly. The aisles were designated to different
product types; air rifle, air pistol, ammo, airsoft, accessories
and more. Each product location in the racks were marked
with a bar code for easy identification while picking an order
for a customer.
To see how fast P/A can process orders, we tagged
along with Warehouse
Manager Todd Bahr as
orders came in. It was
a good thing that we
had sneakers on as we
chased behind him as
he was quickly going up
and down aisles picking
items. The use of high-
tech equipment greatly
aided him in processing
orders from the time
orders come in, to the
time the item(s) is
shipped.
After our
time with Todd, we
understood how P/A is able to ship most orders the same
day, if the customer orders before noon Eastern time.
The next stop was to the airgun repair area where we
met with Gene Salvino, P/A’s Senior Technician. Gene showed
us around the shop. Each airgun smith had an impressive
array of parts, tools and equipment to repair most any type
of airgun. After a short time with Gene, it felt like home to us
swapping different ideas and repair techniques.
Since many at P/A are airgun enthusiasts, we took the
opportunity to show off a few of our customized airguns that
we had brought. About that time, Josh Ungier, the owner and
CEO came to meet us. After checking out our customs and
giving us some shooting tips, Josh invited us to his office to
talk airguns.
Josh’s office was something to see. As you can
imagine, there were numerous airguns in his office. You can
tell his passion for airguns as Josh showed us airguns ranging
from a Crosman 150 to a mint in box one of a kind airgun
that never made it to production. The walls were lined with
various items, including a picture of his parents.
We must admit, upon pulling up to Pyramyd Air’s
new facility in Solon Ohio, we were not quite sure how long
our visit at Pyramyd Air would last or exactly what we’d see
inside. But we were sure excited!
Upon entering the reception area, what was instantly
noticed was that the building was huge and had plenty of
room for future growth.
Marketing Specialist, Stormie VanMeenen greeted
us and
guided us
to our first
stop, the
warehouse.
This massive
58,000
square foot
area of the
building
contains over
4,000 sellable SKU’s.
Walking up and down the numerous aisles of
products was a treat. There were so many products that we
would like to buy, we wished we’d brought a shopping cart
and had higher credit card limits.
Imagine seeing all the products that you’ve only
viewed
online or in
catalogs right
in front you.
The colorful
boxes almost
begged us
to open the
package
to see the
product in
person.
Pyramyd Air’s 70,000 square foot facility.
Shelves packed
with AirForce,
HatsanUSA, Daisy,
and other brands
of air rifles. (Top)
More shelves
packed with
Umarex and more
brands of air pis-
tols. (Bottom)
Todd Bahr picking an order.
Pyramyd Air Owner & CEO: Joshua Ungier.
by Tim Smith
(Cont. on page 28)